How Computer Integration can Upskill the Manufacturing Workforce
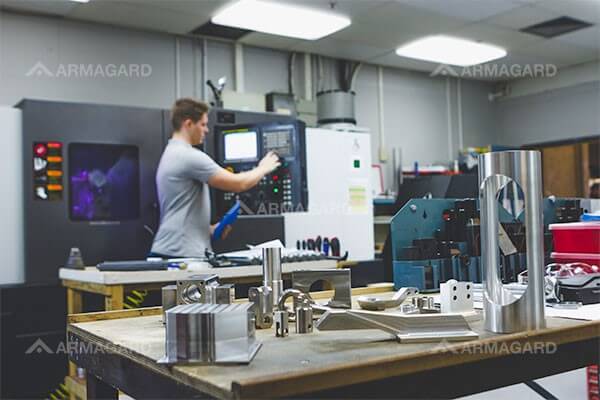
An article published in the Wall Street Journal on September 1st claims that the number of unfilled manufacturing jobs is the highest it's been in 15 years. Why? Apparently, many workers no longer possess the skills to perform today's manufacturing jobs. How can Computer Integration remedy this?
An excerpt from the aforementioned Wall Street Journal article highlights a chronic problem plaguing modern manufacturing operations... computer integration on the manufacturing floor and the loss of jobs.
Commenting on the evolution of the industry, Gary Miller, Director of Training at Ohio-based Kyocera SGS Precision Tools Inc. said: “In 1989, the company employed 550 production workers.
We shed 50% of the workforce over time, producing twice as much thanks to higher-skilled employees and investing in computer-controlled machine tools costing upwards of $500,000 each.”
However, by sacrificing members of the manufacturing workforce, to replace them with computer-controlled systems, Kyocera found itself left with a very big skills gap. Now, by their own admission, they 'struggle to find workers' to operate and maintain those computer systems brought in to improve manufacturing productivity.
What happens when they break down? It's likely they have to call in a specialist engineer, at great expense, because they can't afford to see such systems remaining idle for too long.
Investment in $500,000 computer systems, not training
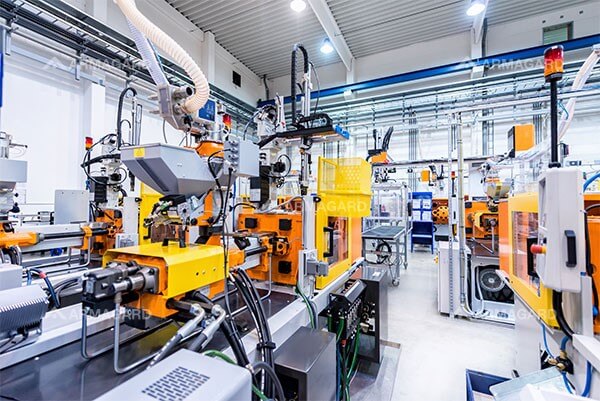
Kyocera are not alone in lacking the essential skills needed to perform the jobs modern manufacturing demands. However, one can't help but think that this problem could have been avoided. What if they sought to train those workers they let go in how to operate and maintain those very computer systems they brought in to replace them?
The fundamental issue here is that some employers in the manufacturing sector seem to think computer integration and the current manufacturing workforce can't go hand-in-hand. Why? It's too costly or it's not sustainable. However, this couldn't be further from the truth. In fact, it's a prime opportunity to upskill the manufacturing workforce.
If companies are taking measures that involve $500,000 investments in just one computer-controlled machine for the sake of improving productivity, why not bring the workforce along by investing in re-training them to work those systems crucial to manufacturing operations?
The result? An in-house workforce that can pass down the necessary skills from generation to generation. In the end, costs are lowered and investing in a $500,000 computer-controlled system can be justified in terms of the total cost of ownership.
Unfortunately, it appears that modern manufacturing practices are determined to take the 'man' out of manufacturing. The problem is, it's all too hasty, especially when manufacturing firms - like Kyocera - encounter skills shortages.
Computer use on the manufacturing floor unfairly criticised

Computer integration has come under heavy criticism recently, blamed for a growing number of job losses, when in reality it creates more jobs. Those jobs are simply going unfilled because the skillset for jobs is changing. We'd be bold as to say that manufacturing jobs aren't disappearing, they just look different to the manufacturing jobs of yesteryear.
The fact is, computer integration can actually serve to enhance the manufacturing workforce. Manufacturing, minus the skills to operate and maintain complex computer systems, equals damage to a lot of bottom-lines.
With that in mind, computer integration should be seen as an opportunity to develop the manufacturing workforce, not replace it. The manufacturing industry can combine efficiency with ethics, while putting an end to the idea that computers are killing manufacturing jobs.
To perfect computer integration on the manufacturing floor, download our free eBook, now...
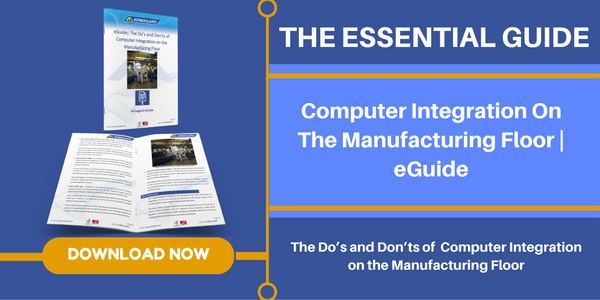
The Wall Street Journal article referred to in this piece was written by Anna Louie Sussman.